Professional Guidance on What is Porosity in Welding and How to Address It
Professional Guidance on What is Porosity in Welding and How to Address It
Blog Article
Comprehending Porosity in Welding: Exploring Reasons, Results, and Prevention Techniques
As experts in the welding industry are well aware, understanding the causes, impacts, and avoidance techniques connected to porosity is essential for achieving durable and trustworthy welds. By diving right into the origin creates of porosity, examining its damaging impacts on weld quality, and discovering efficient prevention approaches, welders can boost their expertise and skills to produce top quality welds constantly.
Common Reasons of Porosity
Porosity in welding is primarily caused by a mix of factors such as contamination, improper securing, and insufficient gas protection during the welding procedure. Contamination, in the form of dust, grease, or rust on the welding surface area, develops gas pockets when warmed, bring about porosity in the weld. Improper shielding happens when the protecting gas, typically utilized in processes like MIG and TIG welding, is not able to fully secure the liquified weld swimming pool from responding with the bordering air, resulting in gas entrapment and subsequent porosity. Furthermore, inadequate gas insurance coverage, typically because of incorrect circulation rates or nozzle positioning, can leave components of the weld vulnerable, allowing porosity to form. These elements jointly contribute to the formation of spaces within the weld, weakening its stability and possibly causing architectural problems. Comprehending and attending to these common reasons are crucial steps in preventing porosity and making certain the top quality and strength of bonded joints.
Results on Weld Top Quality
The existence of porosity in a weld can substantially compromise the general quality and integrity of the bonded joint. Porosity within a weld creates spaces or cavities that deteriorate the framework, making it more prone to breaking, deterioration, and mechanical failing. These voids function as stress concentrators, decreasing the load-bearing capability of the weld and increasing the probability of early failure under used stress and anxiety. On top of that, porosity can additionally act as prospective sites for hydrogen entrapment, additional intensifying the destruction of the weld's mechanical properties.
Furthermore, porosity can impede the effectiveness of non-destructive testing (NDT) methods, making it challenging to spot other issues or stoppages within the weld. This can bring about considerable safety and security worries, particularly in critical applications where the structural stability of the welded elements is paramount.

Prevention Techniques Introduction
Provided the harmful influence of porosity on weld top quality, effective prevention methods are crucial to maintaining the structural honesty of welded joints. Among the key prevention techniques is comprehensive cleaning of the base materials prior to welding. Contaminants such as oil, oil, rust, and moisture can add to porosity, so guaranteeing a clean job surface is crucial. Correct storage space of welding consumables in completely dry problems is also critical to stop dampness absorption, which can cause gas entrapment during welding. In addition, choosing the suitable welding criteria, such as voltage, existing, and take a trip speed, can assist decrease the threat of porosity formation. Making sure appropriate securing gas flow and coverage is another essential avoidance technique, as not enough gas protection can cause climatic contamination and porosity. Proper welder training and qualification are vital for applying preventive actions efficiently and consistently. By including these prevention techniques right into welding practices, the event of porosity can be dramatically minimized, bring about more powerful and extra dependable bonded joints.
Value of Appropriate Protecting
Appropriate securing in welding plays an essential function in protecting against climatic contamination and making sure the honesty of bonded joints. Shielding gases, such as argon, Continued helium, or a mixture of both, are generally utilized to secure the weld swimming pool from reacting with components airborne like oxygen and nitrogen. When these responsive components enter into call with the warm weld pool, they can cause porosity, leading to weak welds with decreased mechanical buildings.
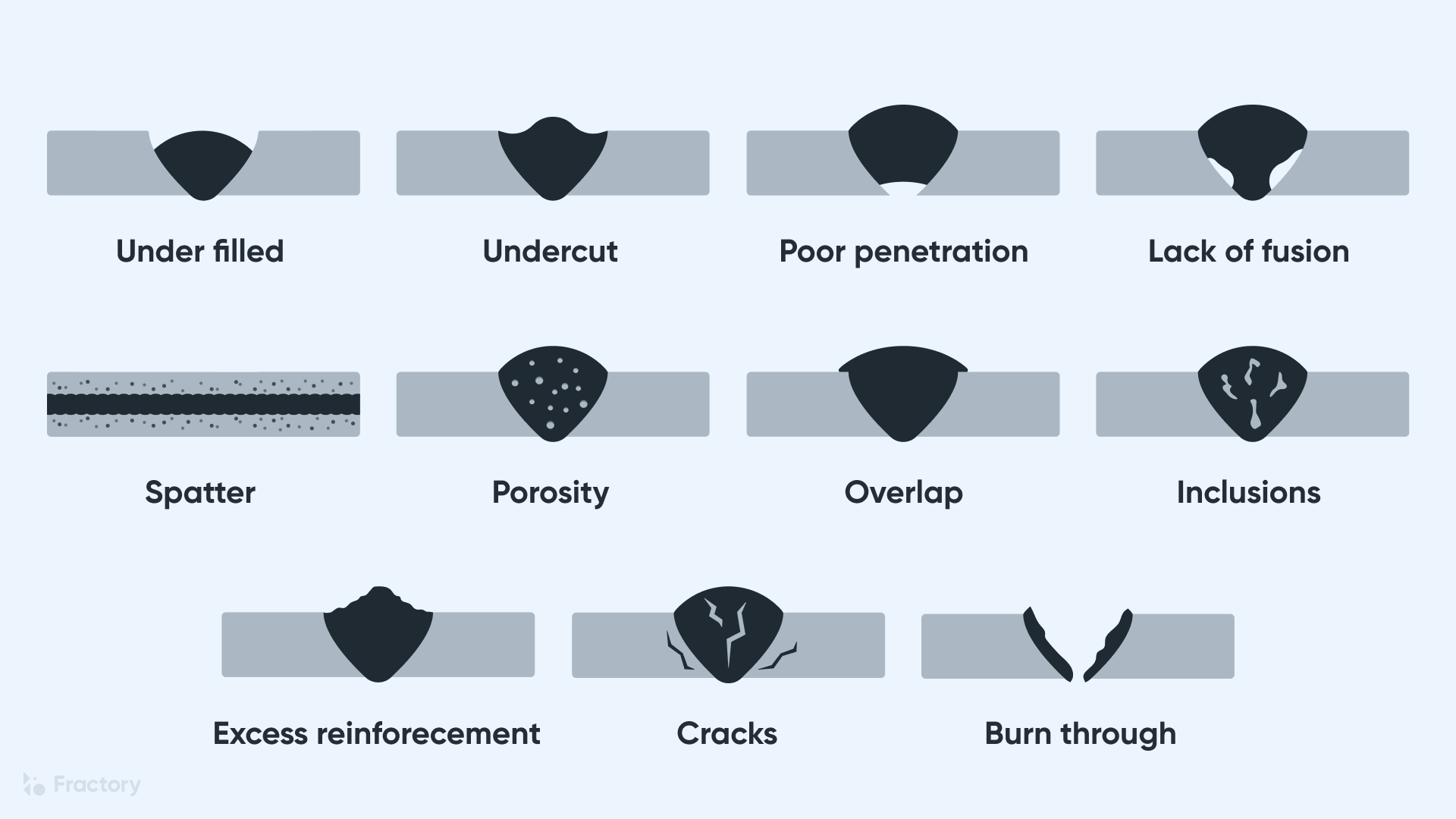
Inadequate securing can cause various issues like porosity, spatter, and oxidation, compromising the structural stability of the welded joint. As a result, adhering to proper shielding techniques is vital to create premium welds with marginal issues and guarantee the durability and integrity of the welded elements (What is Porosity).
Tracking and Control Methods
Just how can welders efficiently keep an eye on and regulate the welding procedure to make sure optimal outcomes and stop issues like porosity? One key method is via the use of sophisticated tracking innovations. These can include real-time tracking systems that provide responses on parameters such as voltage, present, travel rate, and gas circulation prices. By continuously keeping track of these variables, welders can determine discrepancies from the perfect problems and make prompt changes to stop porosity formation.

Additionally, carrying out proper training programs for welders is essential for keeping track of and managing the welding procedure successfully. What is Porosity. Informing welders on the significance of preserving constant criteria, such as correct gas securing and take a trip speed, can assist avoid porosity problems. Normal assessments and certifications can also click resources guarantee that welders are competent in surveillance and regulating welding processes
In addition, using automated welding systems can boost tracking and control capabilities. These systems can specifically regulate welding criteria, lowering the probability of human error and making certain consistent weld top quality. By incorporating sophisticated monitoring innovations, training programs, and automated systems, welders can efficiently keep an eye on and regulate the welding process to reduce porosity issues and attain high-quality welds.
Conclusion
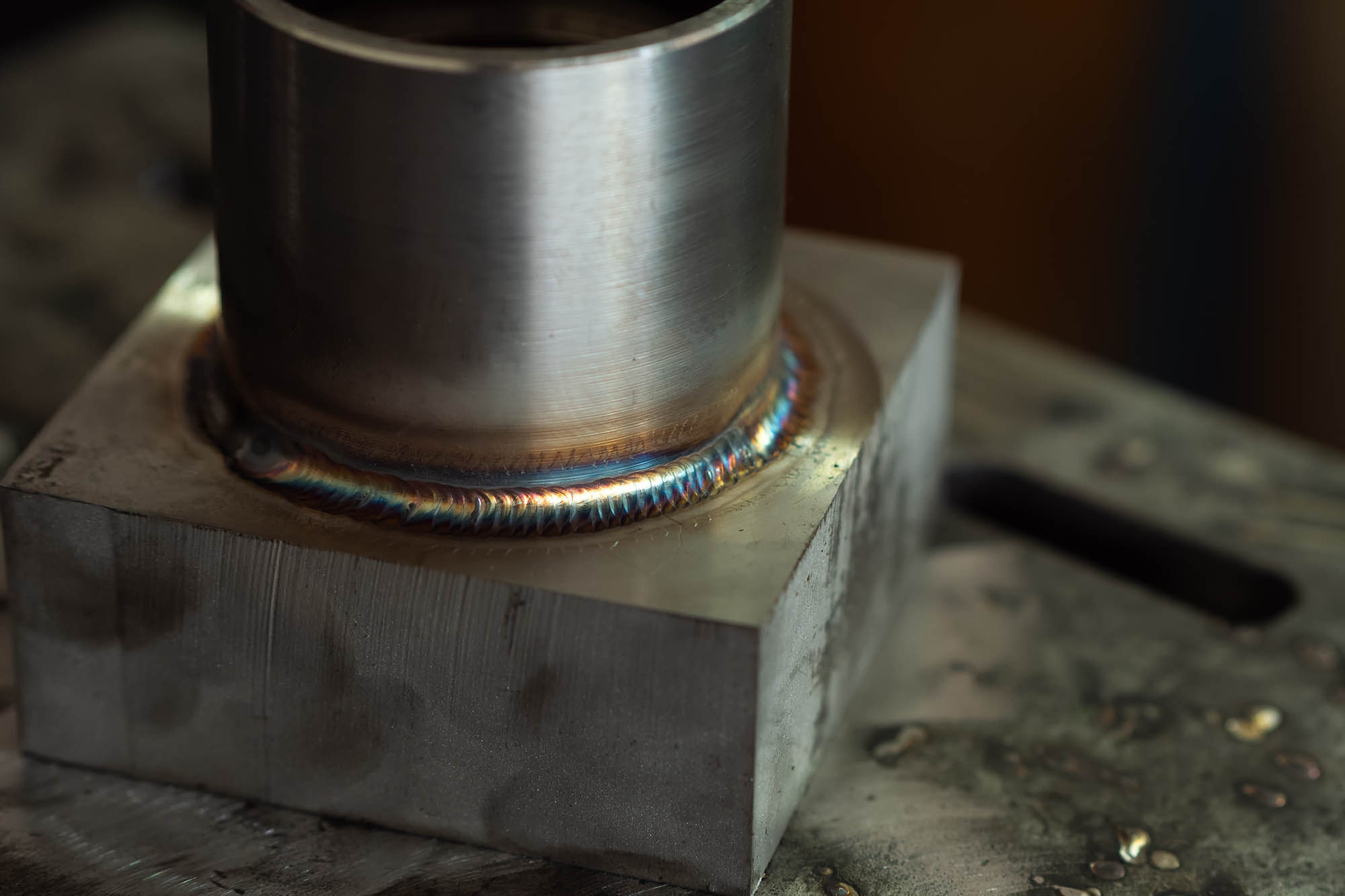
Report this page